Magnesium alloy parts process manufacturing can be carried out on a small machine tool for manual actual operation; when a large number of efficiency is produced by a magnesium alloy part, a special type of large medium automation equipment CNC machining or electronic computer CNC lathe will be more economical. Share the monitoring of the processing of the lower magnesium alloy parts.
The magnesium alloy having a good cutting performance is highlighted compared to metal materials that are poor mechanical processing. For magnesium alloys, strong cutting can be performed at high cutting speed and large feed, which can be reduced.
Unsafe factors during the machining process:
During the machining of magnesium alloys, the incurred chips and fine powders have a risk of burning or explosion. The chip size produced during the initial processing stage is large. Since the thermal conductivity of magnesium is high, the frictional heat generated can be rapidly dispersed, so it is difficult to achieve the thermal point temperature, and this stage occurs less. However, in the finishing stage, since the resulting fine chips and fine powder have a large specific surface area, it is easy to achieve the ignition temperature and cause combustion or explosion accidents.
During the machining of magnesium alloys, the incurred chips and fine powders have a risk of burning or explosion. The chip size produced during the initial processing stage is large. Since the thermal conductivity of magnesium is high, the frictional heat generated can be rapidly dispersed, so it is difficult to achieve the thermal point temperature, and this stage occurs less. However, in the finishing stage, since the resulting fine chips and fine powder have a large specific surface area, it is easy to achieve the ignition temperature and cause combustion or explosion accidents.
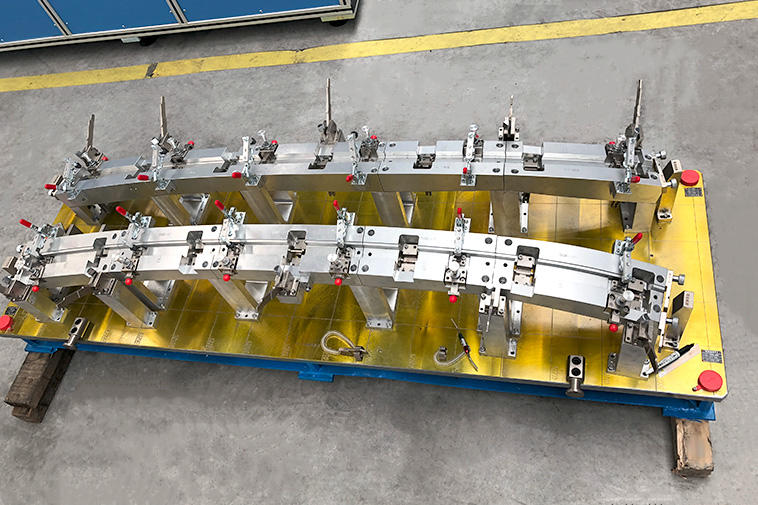
What are the precautions for the processing of magnesium alloy parts
During the processing of magnesium alloys, the influencing factors of the inchelation of the chip to reach the flash or combustion are as follows:
a. Relationship between processing speed and cutting rate. Under any set of given conditions, there is a range that may cause combustion speed and feed rate range. The feed rate is increased, and the chip thickness is increased, so that it is not easy to reach the fuel point temperature. The processing speed is as low enough, and the chips of any size is impossible to be ignited. If the machining speed is high enough, since the contact time of the chips and the tool is short, it is impossible to heat the chips of any size to the ignition temperature.
b. The relative temperature of the environment. The higher the relative temperature, the greater the possibility of firefighting.
C. The composition and state of the alloy. Single-phase alloys are not easily fired compared to multiphase alloys. The more uniform alloy state, the smaller the possibility of firefighting.
d. Other factors. The feed rate is too small; the pause time during the processing is too long; the rear angle of the tool is too small; the cutting speed is used without cutting fluid; tool and nested When the heterogeneous metal core lining in the casting collided, sparks may be generated; magnesium chips accumulate around or below the machine.