(2) whether the first processing of high-precision parts, or periodic repetitive processing of high-precision parts, processing must be in accordance with the drawing process, procedures and tool adjustment card, tool-by-knife, paragraph-by-paragraph program check and verification, especially for the program tool length compensation and radius compensation, if necessary, then do a test cut.
(3) precision machining single-segment test cutting, fast multiplier switch must be placed in a lower gear.
(4) when each tool is used for the first time, it must first verify whether its actual length matches the compensation value given.
(5) in the program operation, to focus on observing several displays on the CNC system.
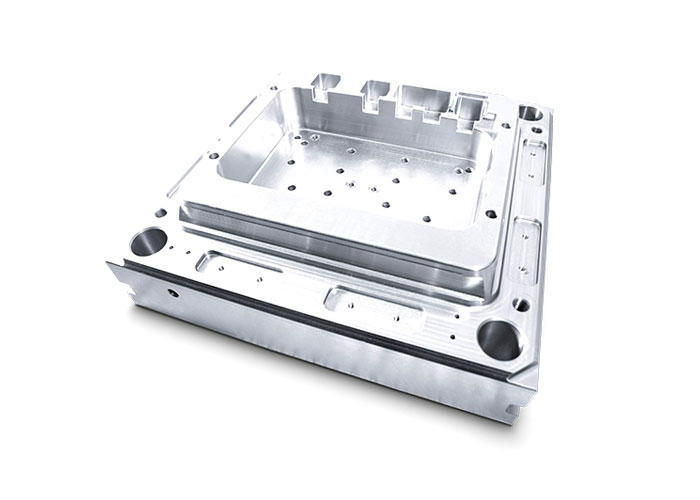
(6) coordinate display: you can understand the current tool movement point in the machine tool coordinate system and the workpiece coordinate system, to understand the movement of this program segment, and how much remaining movement, etc..
(7) register and buffer register display: you can see the contents of each status instruction and the next program segment of the program segment being executed.
(8) Main program and sub-program display: High-precision workpieces can see the specific contents of the program segment being executed.
(9) dialogue display (Custom): can understand the machine tool current spindle speed, the current cutting feed speed, spindle cutting feed per revolution, spindle current cutting load and each stroke axis load spindle cutting feed per revolution to calculate the corresponding tool cutting volume per edge.
(10) high precision parts test cutting into the tool, in the tool running to the surface of the workpiece 30 ~ 50 mm, must be maintained at a low speed feed to verify the remaining coordinate axis coordinate values and X, Y axis coordinate values and drawings are consistent.
(11) for some of the tool test requirements, the use of "progressive" method. For example, for boring precision parts, a small length can be bored first, and then the whole length can be bored after passing the test. Use the tool radius compensation function of the tool data, from large to small, while trial cutting and modification.
(12) In test cutting and precision machining, after replacing the tool and auxiliary tools, be sure to re-measure the tool length and modify the tool compensation value and tool compensation number.
(13) program retrieval should pay attention to whether the cursor refers to a reasonable and accurate position, and observe whether the coordinates of the tool and machine direction of motion are correct.
(14) After the modification of the high precision workpiece program, the modified part must be carefully calculated and carefully checked.
(15) hand crank feed and manual continuous feed operation, you must check whether the position selected by the various switches is correct, clarify the positive and negative direction, identify the keys and set the feed rate or pulse multiplier, and then operate.