Ceramic mold casting is a new process developed on the basis of ordinary sand casting. It is mainly used for casting large-scale thick-walled precision castings and casting single-piece and small-batch punching dies, forging dies, plastic dies, metal dies, die-casting dies, glass dies, etc. The service life of ceramic casting molds is comparable to that of molds made by machining methods, and the manufacturing cost is lower than that of molds made by machining methods.
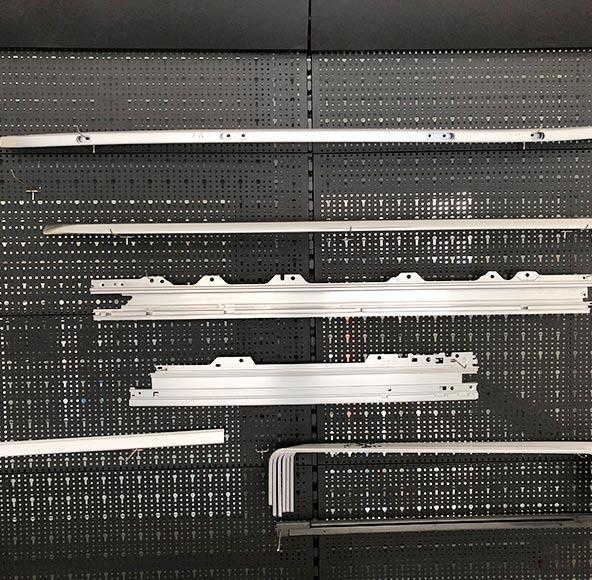
When the wet type cannot meet the requirements, consider using the clay sand surface dry sand type, dry sand type or other sand type. The weight of castings produced by clay wet sand casting can range from a few kilograms to tens of kilograms, while the castings produced by clay dry casting can weigh tens of tons. The density, metallographic structure, and mechanical properties of the material are often poor, so when these properties of the casting are required to be higher, other casting methods should be used.
Such as investment (lost wax) casting, die casting, low pressure casting and so on. The production efficiency of solid molding is high and the floor space is small; for the middle parts, various high-pressure molding machine production lines and air punch molding lines can be selected to meet the requirements of fast and high-precision molding production lines. The core-making methods can be selected: Efficient core making methods such as cold core box, hot core box and shell core. The pit modeling method is low in cost and quick in production.
For mass-produced or long-term shaped products, it is more appropriate to use multi-box modeling and split-box modeling. Although the initial investment in molds and sand boxes is high, it can be compensated by saving modeling time and improving product quality. A preliminary cost estimate of the casting method selected should be carried out to determine a casting method that is economical and can meet the requirements of the casting.